Robert M. Hotter, Hotter GmbH, Chemical Products, Austria
Abstract
This article addresses the challenge of maintaining plate heat exchanger (PHE) efficiency in industries like papermaking, where they are key energy recovery tools. Over time, deposits reduce efficiency, waste energy, and increase costs without proper cleaning
Introduction
PHEs consist of plates with rubber seals pressed together between two thick end plates, forming channels for two separate liquids to flow and transfer heat efficiently.
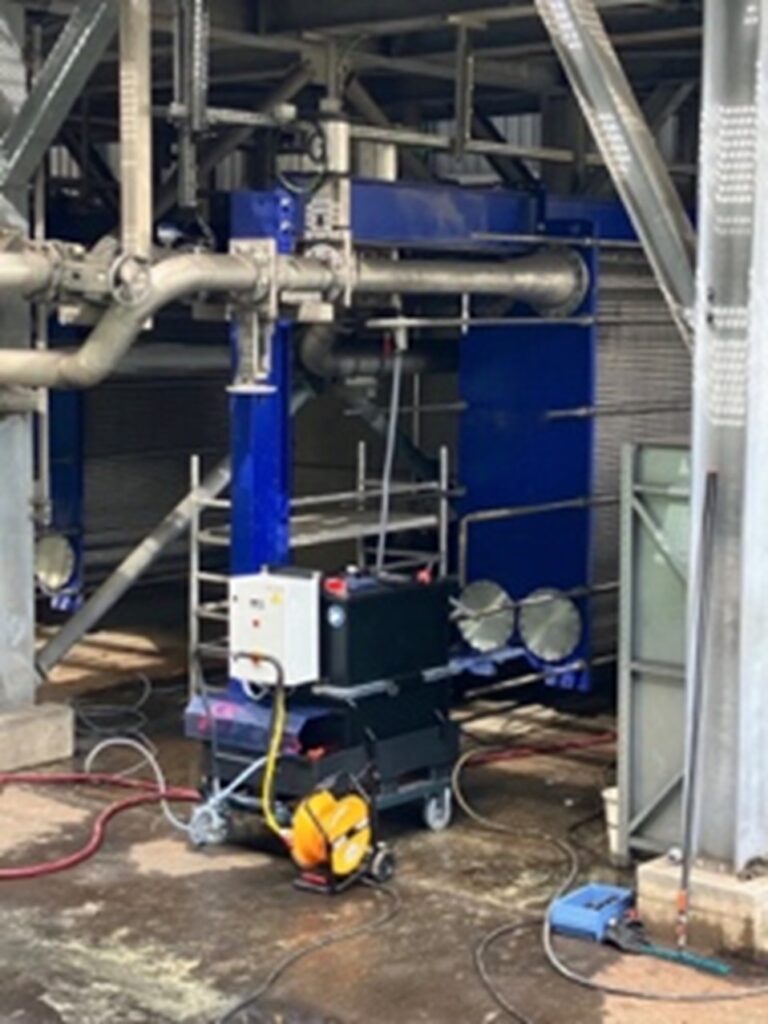
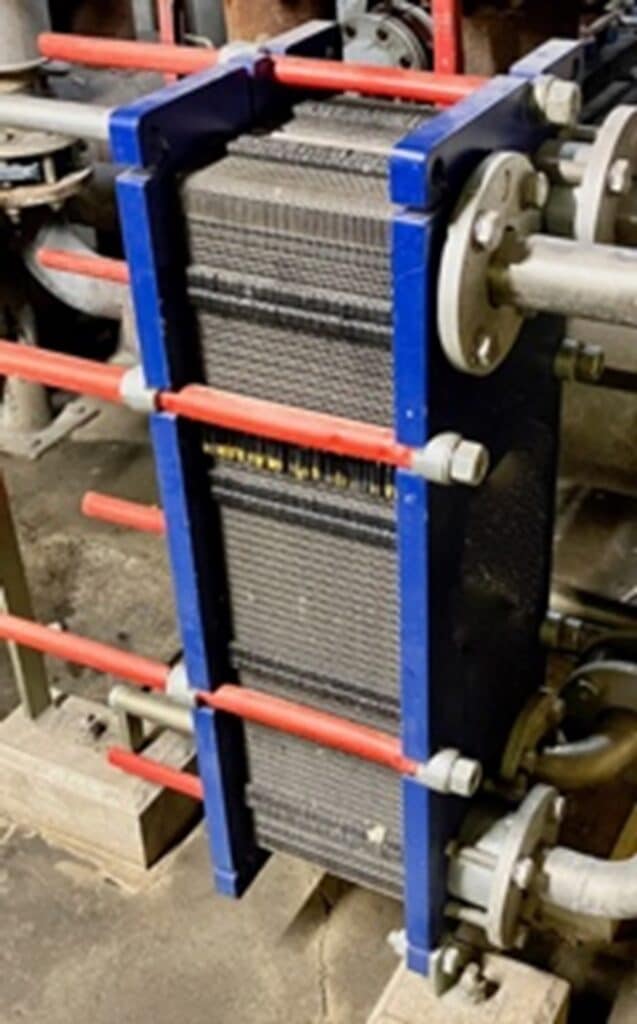
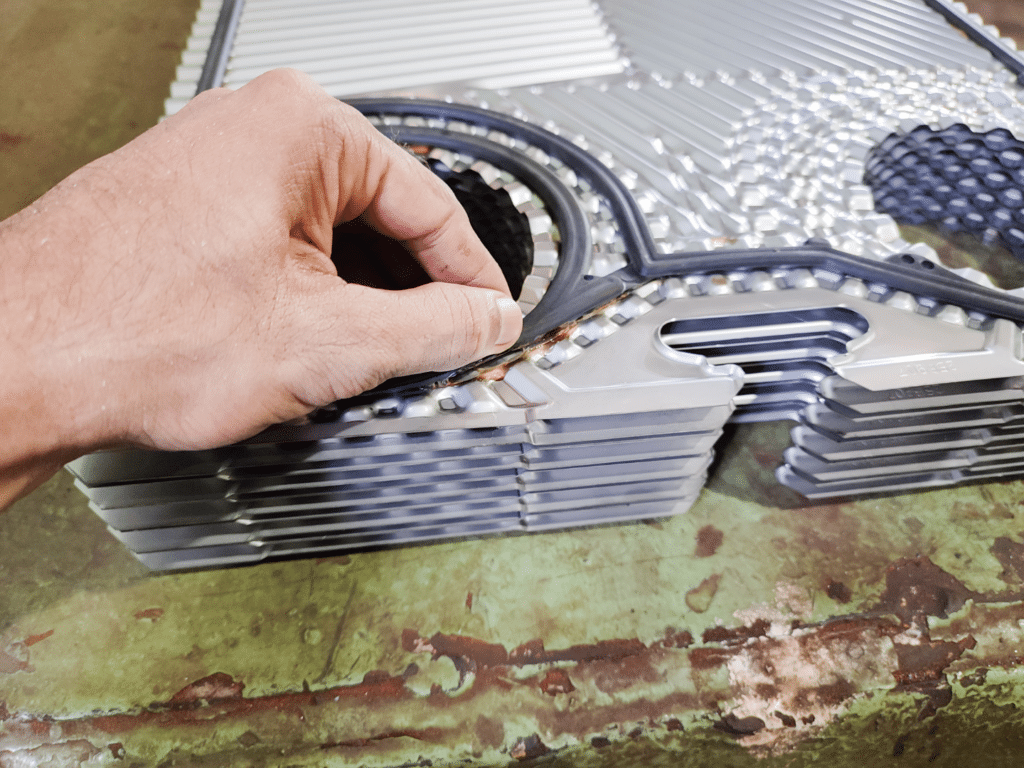
Current Cleaning Methods
Factories clean PHEs during annual shutdowns by disassembling the entire plate pack. Plates are removed, washed or immersed in chemical baths, and rubber seals replaced. This process can take two workers up to a week, incurring:
- High labor costs.
- Significant downtime.
- Risk of damage during handling.
Fouling often reoccurs within weeks, reducing efficiency to 50% or less well before the next shutdown.
Mechanical disassembly & assembly takes 2 men up to one week with the risk of damages.
The Solution: Flushing Without Dissassembly
Flushing the PHE without disassembly can prevent efficiency losses. Usually, the deposits are based on minerals in the water, like carbonate or manganese and iron. Chemical flushing effectively removes deposits by circulating heated cleaning chemicals in a closed loop through the PHE, dissolving buildup and restoring heat transfer efficiency
HeatFlow Pro: A Smarter, Safer Solution
The HeatFlow mobile unit allows factory staff to clean PHEs efficiently on-site anytime.
- 480-liter chemical tank, adjustable heating, and reversible flow for thorough cleaning.
- Flushing of both hot and cold plate sides.
- Four-wheeled cart with an acid-resistant catch pan.
- Efficient, safe and sustainable cleaning agents from Hotter GmbH.
CE-certified and user-friendly, HeatFlow Pro simplifies flushing and includes easy rinsing to remove residues.
Real Results: Eficiency Restored In Hours
Our HeatFlow Pro has been used on huge PHE with a volume of 2,5 m3 and also on smaller versions with only 100 liter as well. Our chemicals have been used and the results are impressive.
After only 2 hours of flushing the heat transfer increased up to 50%. Our customer is extremely happy with the handling of the unit and naturally with the results of the flushing.
Now their target is to keep the level of heat transfer as high as possible until the next annual shut down. After the next rebuild of the PHE pack of plates, our customer plans to keep the heat transfer at the level of the newly rebuilt PHE by flushing frequently.
In the end they hope to avoid the annual rebuild alltogether, or at least increase the time between rebuilds to 2 years or more.
Conclusion: Modernize Your PHE Maintenance
Regular flushing with the HeatFlow Pro helps maintain peak PHE efficiency and extend intervals between rebuilds. This approach reduces downtime, lowers costs, and may even eliminate the need for annual rebuilds altogether.